Protecting the contents is an essential element in food and beverage packaging, meeting the current requirements of the consumers’ lifestyles. There has been innovation in the thoughts and ideas of packaging such as simplified packaging for fresh foods that eliminate trays and beverages in spout pouches, but the strength required to withstand transportation and storage and cater to limited display space is the central premise in packaging. This first series focuses on strength testing of food packaging and beverage containers with measurement examples of “Compressive Strength” among strength tests.
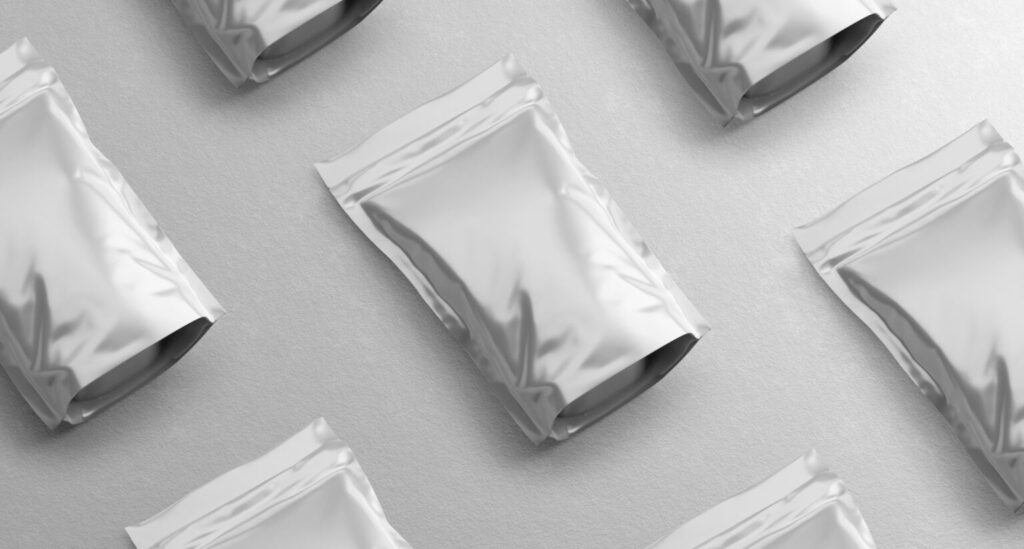
Top Load Test for PET Bottles
The top load test is one of the most common quality control tests for PET bottles.
In the top load test (buckling strength test) on PET bottles, the compressive force when bent is measured by crushing the PET bottle directly from above using a force gauge or top load testing instrument. Managing buckling strength is extremely important in terms of durability against stacking during transportation and storage and in terms of avoiding problems during the filling and capping processes.
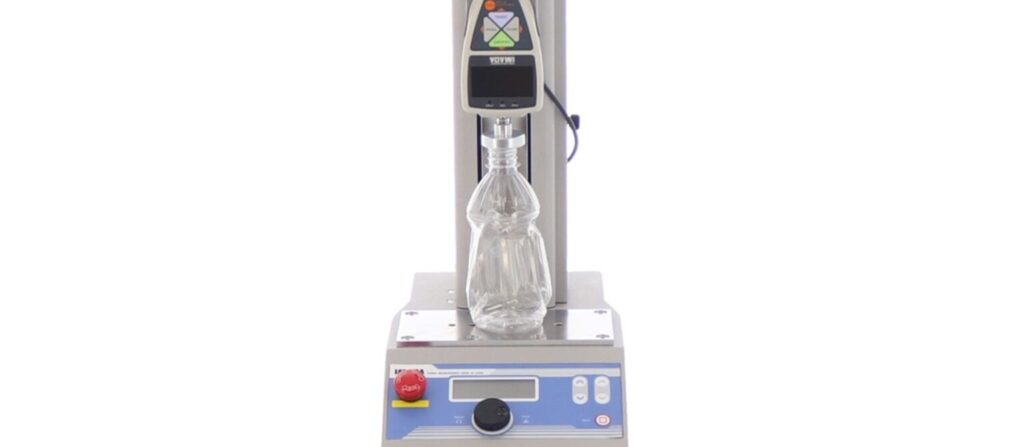
Top load tests on PET bottles are generally performed with the newly manufactured empty bottle without the cap before filling to measure the actual container strength. The jig with slots for air escape is used for compression. The measurement results differ, with or without the cap or the compression jig differences, even if made in the same manufacturing environment.
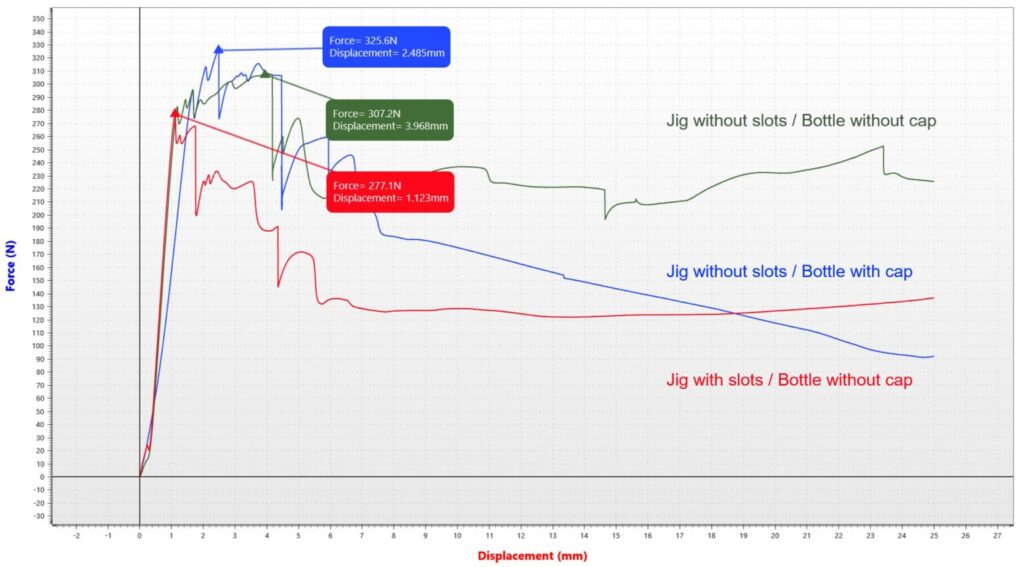
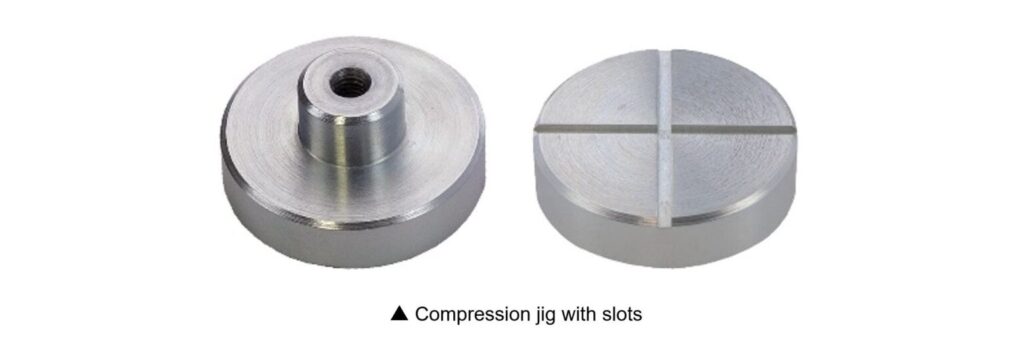
The lower buckling bottle strength means a higher risk of denting and breakage, especially during transportation and storage, and on the other hand, should have the advantage of the ease of crushing after consumption.
In the recent industry trend, some products have been manufactured intentionally with reduced buckling strength. In any case, it is essential to determine and manage the buckling strength most appropriate for each product.
Compressive Strength Test of Retort Pouch Packaging
The next is a compressive strength test for retort pouch packaging.
Retort pouch is a type of packaging sealed airtight by welding, and compression resistance tests are used to evaluate the welding adhesion level. In the test, a content packed retort pouch is compressed under a constant force for a certain period to see if any damage or the content leaks. There are no set rules on the load or time, but for example, The Japanese Industrial Standard JIS Z0238:1998: Test method for heat-sealed flexible packaging bags and semi-rigid containers “10. Compressive strength test” states that a load(force) determined by the number of contents for 1 minute. It is important to compress the entire container so that the load is firmly applied to the welded parts equally, when compressing.
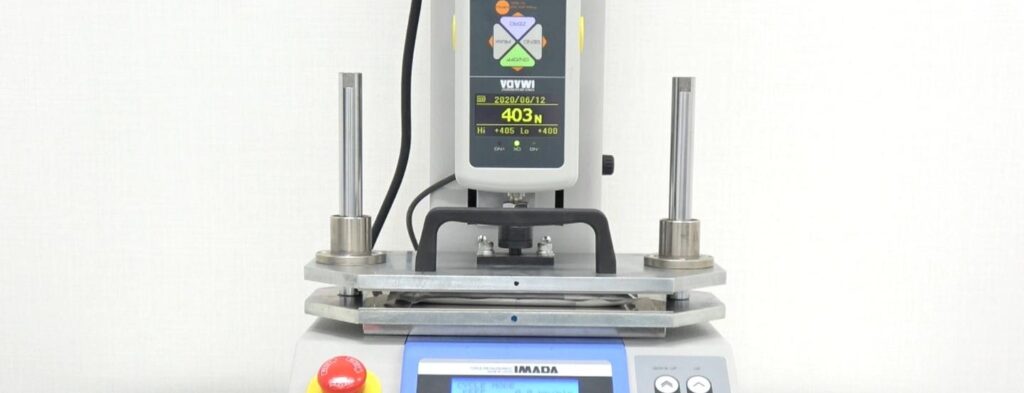
A similar compressive strength test applies to strength tests of paper and corrugated cardboard boxes used for packaging for transportation and storage. In particular, the strength of packaging materials (e.g., corrugated cardboard) significantly impacts durability against stacking with transport and storage. Strength control is necessary to protect the safety of the products, including the individual inner boxes in which the products are packed in an appropriate condition.
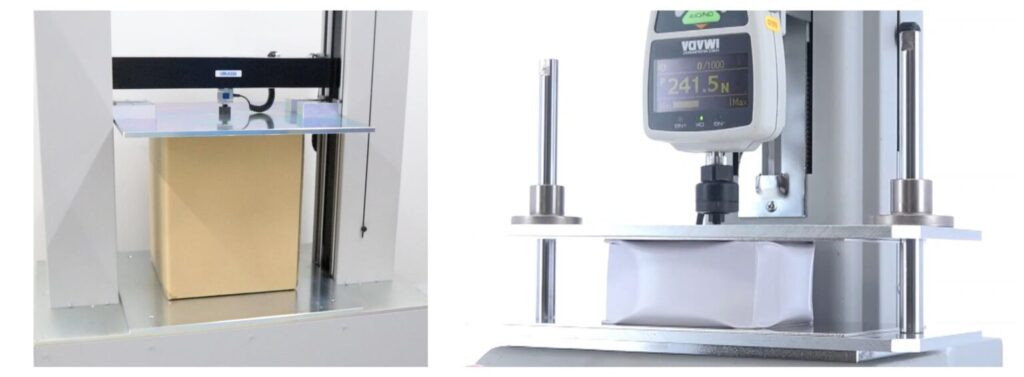
Packaging Film Puncture Resistance Test: Puncture Strength Test
The last test introducing is the Puncture Resistance / Puncture Strength Test of packaging films.
While the previous compressive strength test applies compressing force to the entire product package, the puncture test proceeded with a pin to apply compressive force to a single point and measure the force required to penetrate the package film. Regarding the standards for puncture strength testing of food packaging films, the JIS Z1707:2019: General rules for plastic films for food packaging, available, which stipulates the size of pins used for puncturing and testing speed. Tests are conducted in film form, not in the packaged form.
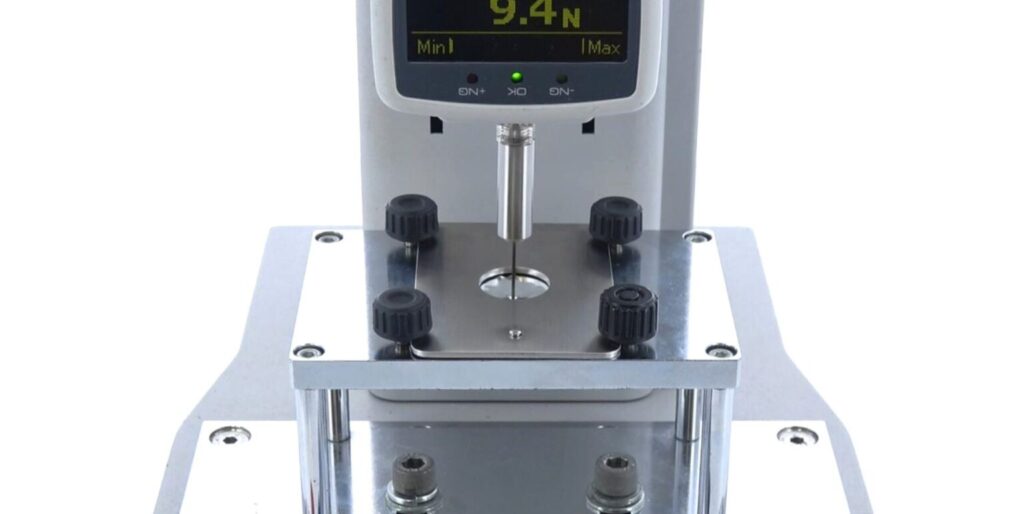
More products are vacuum-packed for extended shelf life. Hence, the quality control of the packaging film is an essential issue. Any hole is created, the vacuum state breaks and the content could leak, causing oxidation, which may lead to molding. The pinhole occurs when the contents, especially hard foods such as nuts and frozen foods, are pressed and rubbed against the film during transportation and unpacking. It is essential to control the state of the film used for packaging. A similar test is applicable for the straw sticking force measurement to a heat-sealed beverage cup container.
Summary
This article (1) introduced compressive strength test examples focused on food and beverage packages.
It is essential to manage and control packaging for the various functions and the purposes of transportation and storage per the necessary standards and regulations to protect and store correctly to avoid any related issues. As mentioned earlier, the packaging’s functions and purpose continue to change, and we hope to provide practical support and consultancy with the product development. If there are any concerns or questions on the measurement, consulting us may be one of the solutions.
IMADA’s website introduces a series of video examples on force measurements. Various topics related to force measurement and power are introduced on the Force Channel. Please also check other articles.
*Click here for some hints and measurement example videos for food and beverage packages and containers.