Those of you in the manufacturing and service industry are probably familiar with the International Standard ISO9001, the Quality Management Systems widely recognized. We were approved and acquired the certification in 2000. Since then, we have been building and practicing our Quality Management Systems (hereinafter, QMS) using ISO 9001 as a foundation to fulfill our Mission of manufacturing and providing additional values and services to our products, contributing to our customers’ manufacturing scheme through force measurement.
We wish to introduce IMADA’s QMS in this article.
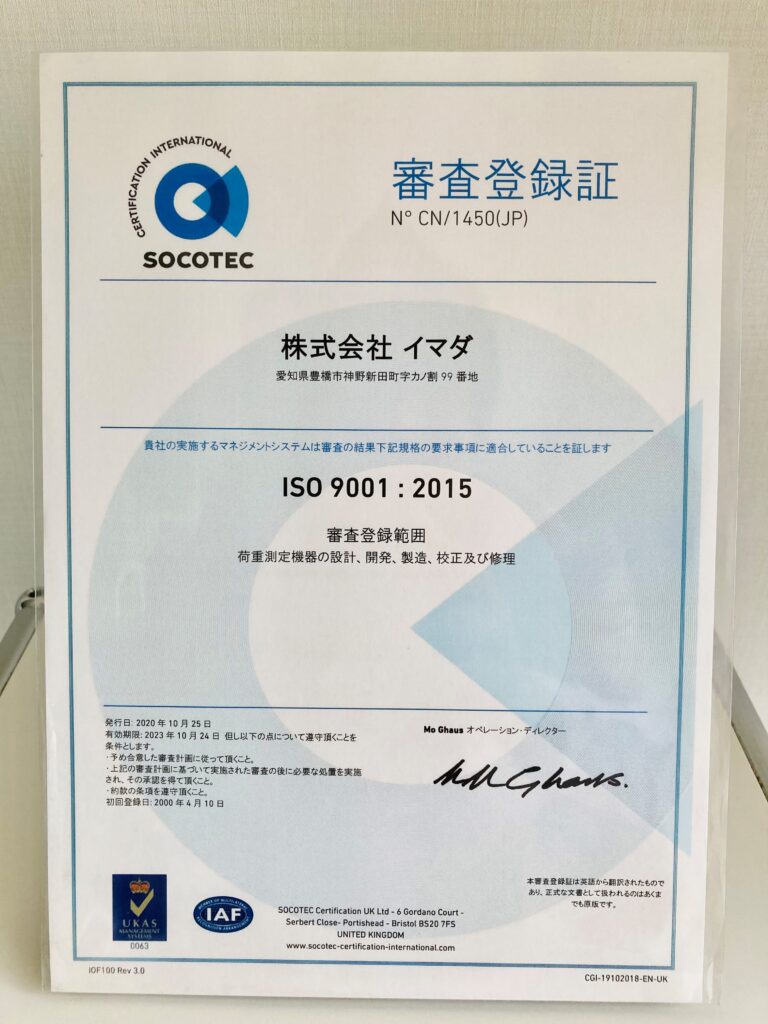
Design, development, manufacture, calibration and repair of force measurement equipment
Communication systems as the basis for corporate activities and management
We have several communication systems to ensure the quality of the company’s products and services.
At the Quality Management Meeting, we confirm the general achievements towards the mid-term management plan set every year.
Our CEO and the management members from each Team cross communicate to share the progress, update the current performance status, and work on better recognizing the value in the process.
Also, twice a year, management review meetings are held to discuss the products standard improvements on the quality and services based on the longer-term management goals.
In this meeting, the management team envisions future customer needs by considering the external business environment and upcoming changes in manufacturing, and designs the mid-term management plan and long-term business goals for the company’s targeting quality to meet those future customer needs.
Internal auditing is also conducted in the management review by the team members involved in cross-team operation for organization development.
These members investigate and research if the team operations and the missions are correctly conducted. In the case of problems investigated, they must support and lead them to work on the problem-solving options. This opportunity also helps deepen the understanding of QMS among these members responsible for the management in the future.
About our Teams and the tasks to conduct appropriate quality management, enhancing customer satisfaction
To manufacture and supply IMADA’s high-quality force measuring instruments and ensure that our customers correctly use them, each team with the clearly defined Mission to conduct the individual tasks.
The following is a brief description of each team’s role in QMS.
The Customer Service Team serves as the point of contact with the customer to handle requests, make the most suitable and optimal product proposals, and process prompt shipments.
The Technical Team is responsible for product development and design, such as creating new products based on market needs and updating existing products, and also responsible for advanced measurement consultations.
The Manufacturing Team maintains high productivity with the controlled, stable quality in various IMADA products. The group is also responsible for repair and calibration, ensuring that our products can plan an active role for a long time.
The Human Resources and General Affairs Team takes care of hiring and training programs rooted in IMADA’s corporate culture and improving the working environment by organizing regulations for the appropriate operations of the QMS. In addition, finances and related transactions are checked with financial efficiency.
The Marketing and International Sales Team provides accurate information on each product, identifies new customers, and establishes the most appropriate sales format for each industry and region.
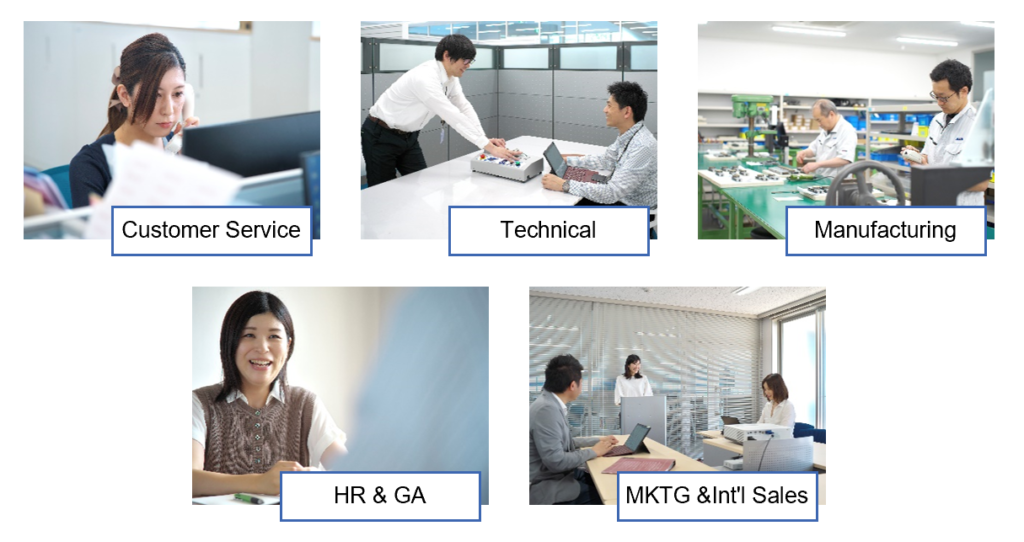
The professional skill evaluation for the all staff and the training system for the manufacturing team members
In order to ensure product quality, continuous improvement of the manufacturing team member’s skill is necessary. Our Education and Training Rules determine some manufacturing tasks as Special Process Tasks and allow only staff who have enough working records and pass the exam to deal with the Tasks. Even after obtaining the qualification and being certified as special process personnel, regular practical checks are conducted to maintain a high skill level.
We also utilize professional skill evaluation systems to assess each member in all groups how much he/she improves necessary skillsets for their tasks.
We have introduced various initiatives related to typical QMC with the Mission. IMADA also practices other regulations to support QMS with a multi-leveled approach. We will continue to make minor improvements daily to meet higher customer satisfaction through effective quality maintenance of IMADA products.