In the previous article, Introduction to Friction Testing (1), we introduced the “friction test of printing paper” as an example of a surface-to-surface contact friction test, which is the simple test method of placing a weight on top of two stacked samples to slide. The friction is not only for surface-to-surface contact or sliding. For example, friction is also generated when a pencil is used for writing letters on paper. The friction shaves the pencil lead, and the shaved lead (graphite) particles adhere to the paper to draw or write letters on the paper.
In this article (2), we introduce another example of friction tests, focusing on the friction force between surfaces and the point (including relatively narrow surfaces) of contact. In physics, maximum frictional force = normal force x coefficient of friction, and the maximum frictional force is not affected by the contact area, but in reality, the maximum frictional force depends on a range of factors, including the contact area, and it fluctuates. Therefore, deciding the test method based on the usage and shape of the sample you wish to measure is essential.
*Click here for the article “Introduction to Friction Testing (1) “Surface-to-Surface Contact Friction Testing.
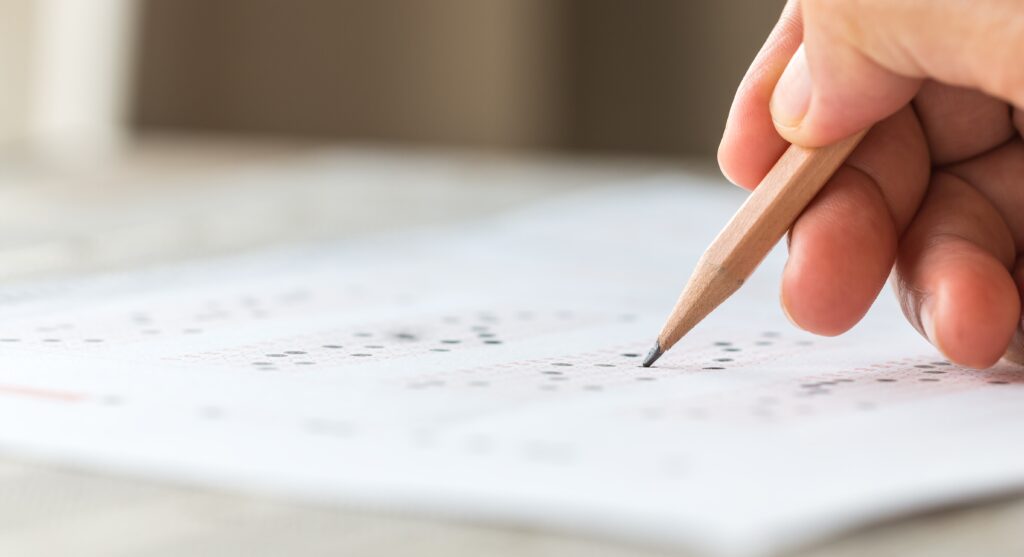
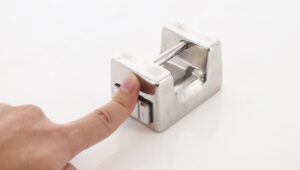
case study #1 Friction test between Eyeliner and the Artificial Skin
The first test is the “Friction Test of Eyeliner and Artificial Human Skin”. Friction tests on the skin are essential, especially in the cosmetics industry, for various purposes, such as measuring the effects of skin lotions, cleansing, and masks. Tests are often conducted with actual human skin, but in this case, we are using artificial skin, and by drawing lines with eyeliner on the artificial skin, we have measured the maximum frictional force and coefficient of friction between the eyeliner and the artificial skin.
We have used the measuring device below: – When the eyeliner is fixed to the stick holder and moved to the left, friction occurs between the tip and the artificial skin set to the table unit sliding section, and the friction force is measured with the force gauge. To create a realistic environment, the eyeliner is slightly tilted so the tip in contact with the artificial skin is at an angle.
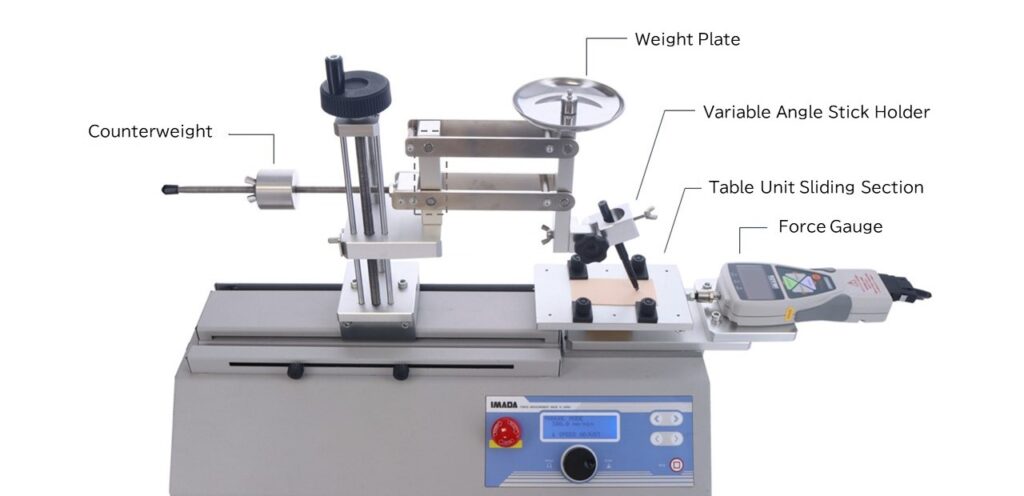
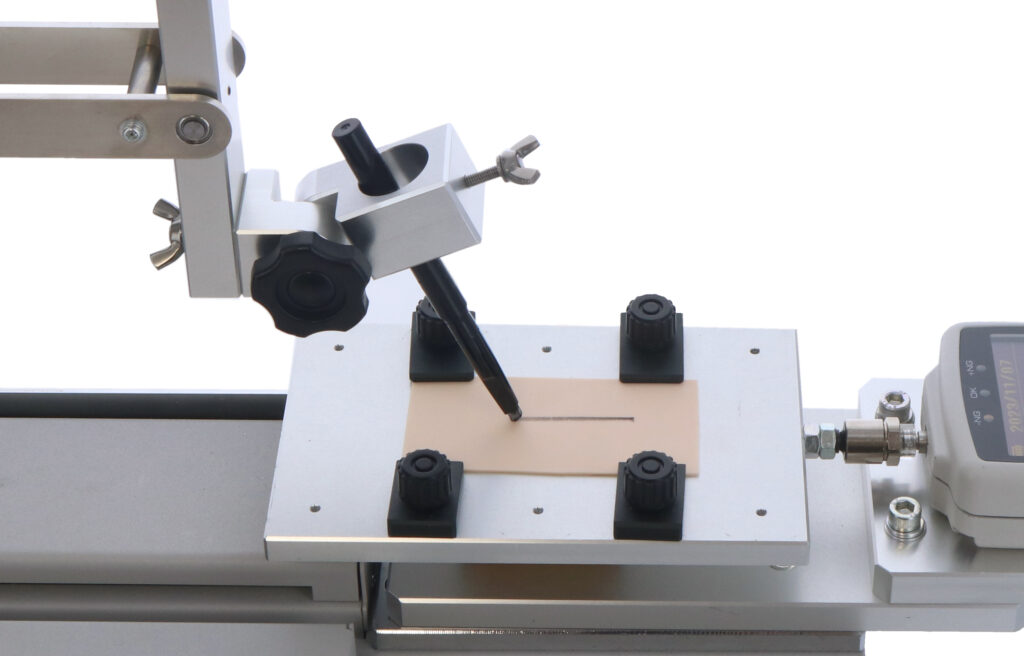
This measurement used two types of eyeliner samples: pencil(solid) and gel (liquid) types, and the results are shown in the graph below. The graph shows that the gel type has a lower static coefficient of friction and lower average dynamic coefficient of friction and that lines are drawn smoothly with lower friction forces.
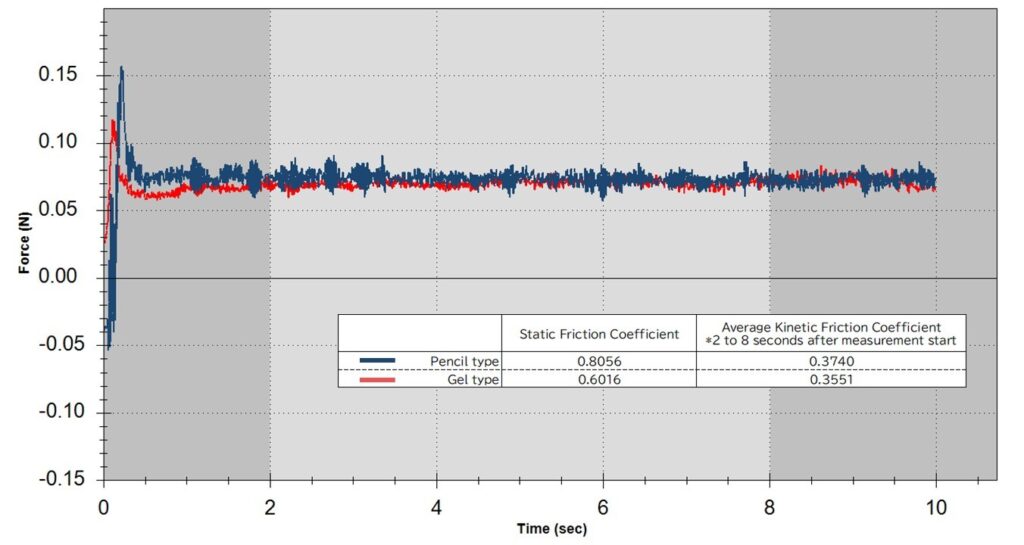
case study #2 Friction Test of Tablet Protective Film and Stylus Pen
Next, we will introduce the Friction Test of Tablet Protective Film and Stylus Pen.
Creating documents and illustrations using digital equipment, such as tablet devices, has become mainstream, and various protective films are available for different purposes. Friction is essential in determining writing comfort, and measuring the coefficient through friction tests is important.
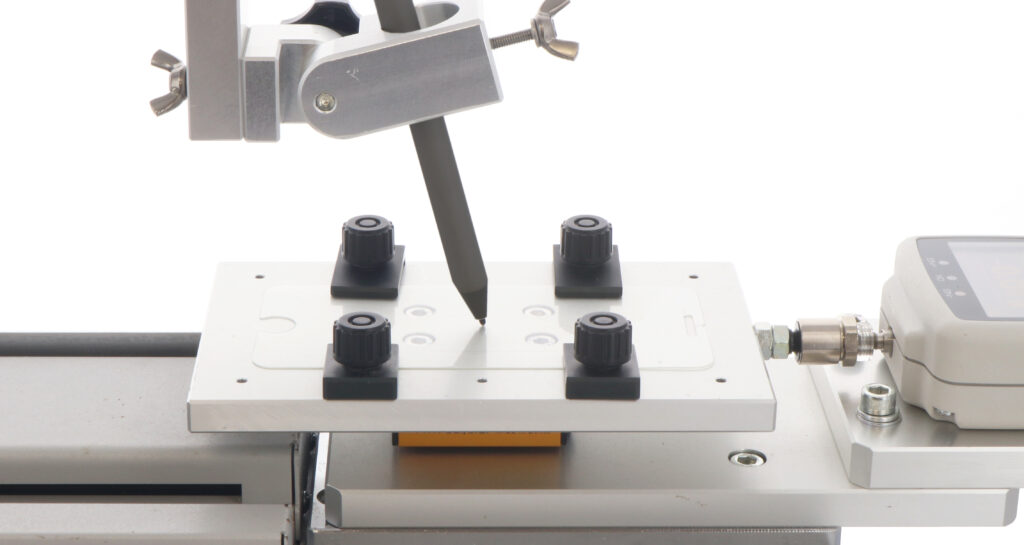
The same instrument was used again for this measurement.
Some stylus pens have functions such as pressure detection, so measuring with multiple weights while changing the weight (normal force) is necessary. The graph below shows the measurement results for weights of 40g/60g/80g; logically, in Physics, the coefficient of friction measurement results should be the same, but inconsistency is identified from the result.
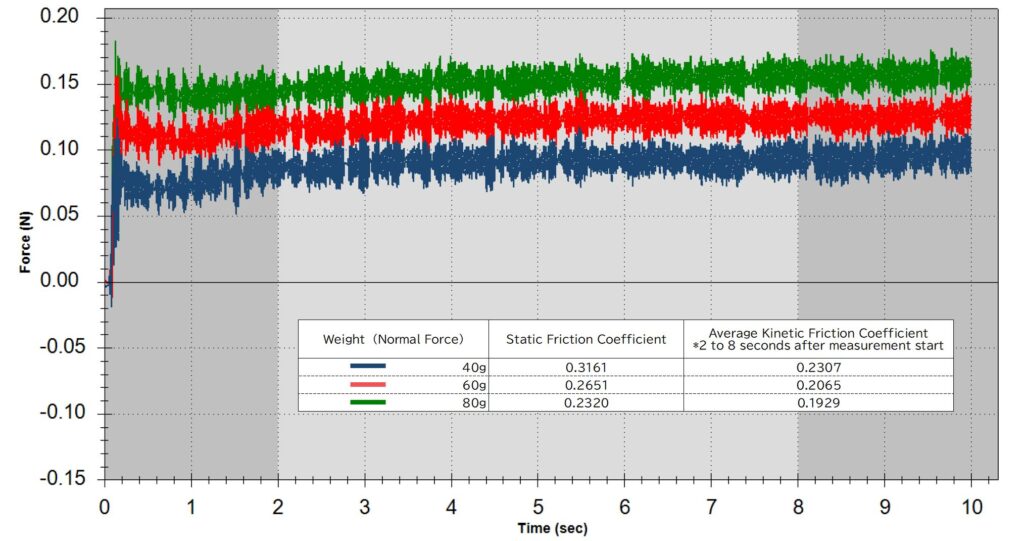
case study #3 Grease Lubricity Test (ball-on-plate method)
The last case study introducing is the “grease lubricity test (ball-on-plate method).” The ball-on-plate method is a test method in which a sphere-shaped product is slid on a plate for measurement, and it is one of the basic friction test methods for wear testing of metallic materials and ceramics, in addition to lubricity testing. Since the contact area between samples is small, the pressure per unit area is large, and stable contact is maintained. Also, it is essential to understand that the contact area widens as the sphere sample wears down.
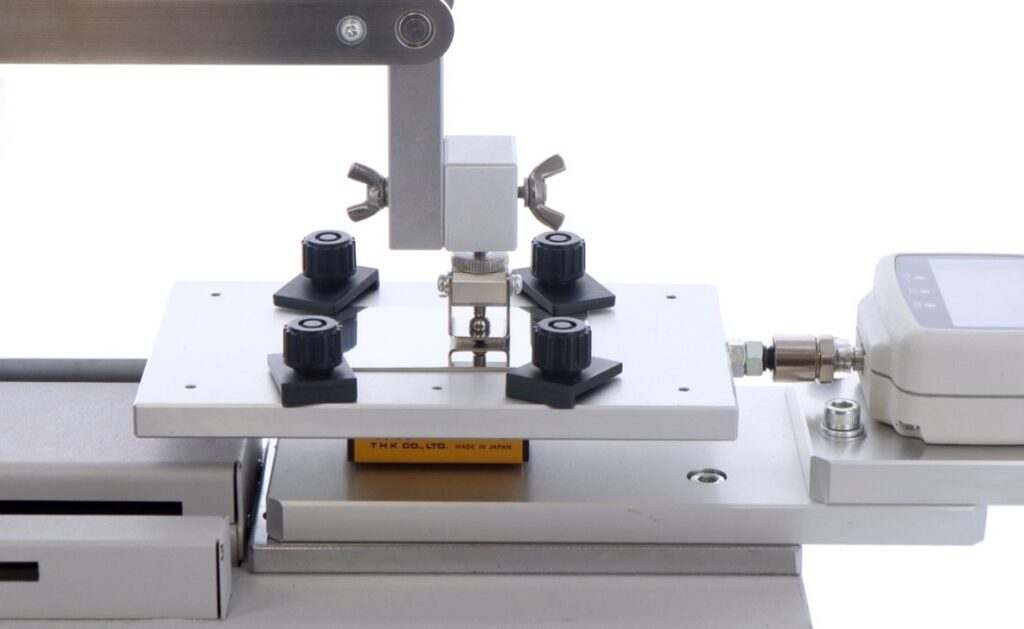
In this measurement, the lubricating effect of grease on stainless steel is measured, the petroleum-based grease is applied to a stainless-steel plate, and the frictional force is measured with the stainless-steel ball slid across the plate. The frictional force without any grease is also measured for comparison.
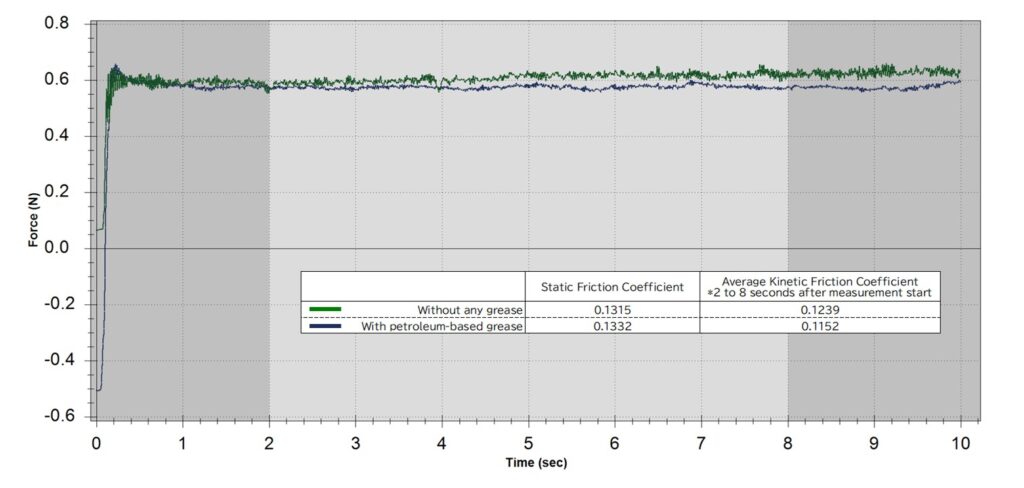
The above graph shows the measurement results. Although the static coefficient of friction has increased slightly, the average dynamic coefficient has decreased due to the grease application. The graph below shows the frictional force of a steel ball after. The average dynamic friction coefficient remains low, indicating that the lubricating property is maintained. In this case, only one grease type is used; for example, different grease comparisons enable the choice of greases appropriate for the requirements.
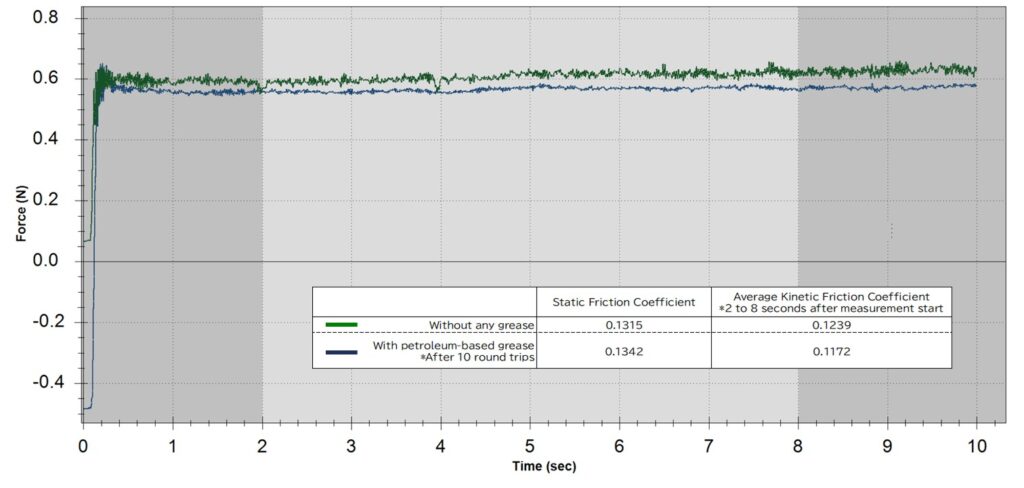
Summary
In this article, we introduced friction tests based on surface and point contact, with the “friction test of eyeliner and artificial human skin,” “friction test of protective film and stylus pen,” and “lubricity test of grease (ball-on-plate method)” as examples. Friction testing by surface-to-point contact is also used for quality control and product development research in various situations, such as measuring writing instrument comfort. As mentioned, frictional force is affected by several factors, such as contact area and angle. Of course, there are limitations depending on the shape of the sample and the testing devices, but it is essential to conduct measurements in a realistic environment.
In the next issue, we plan to introduce abrasion tests as a “test to observe changes from repeated friction”.
The Force Channel is our platform, introducing various Force and Chikara measurement articles. Please check other articles.
Measurement example videos from the following links: –
Coefficient of Friction Measurement for Writing Materials
Coefficient of Friction Test for Lubricant (Ball-on-Plate Test)
*Note
The results stated are based on the sample measurement proceeded for this particular article. The results vary depending on the actual samples and the measuring environment.