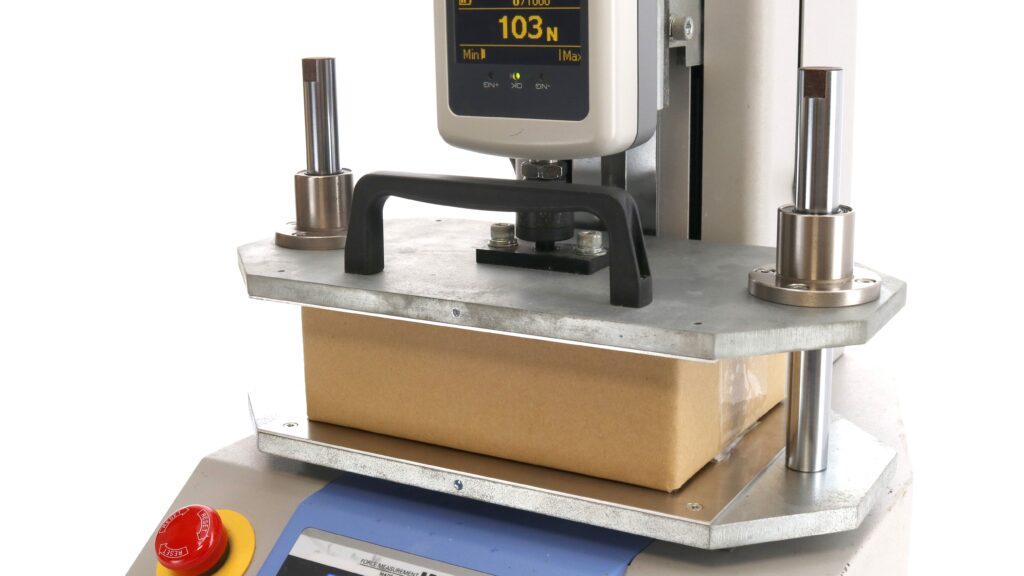
圧縮強度、機能性を評価する圧縮試験
圧縮試験とは、サンプルに圧縮方向(押し込む、押し潰す)のチカラを加えて、強度や操作性などを確認する試験です。サンプルに加えられたチカラを測定するため、荷重測定のひとつに分類されます。圧縮試験の目的は、大きく「圧縮強度の確認」と「機能性の評価」の2つです。
- 圧縮強度の確認:サンプルの物的特性である強度そのものを確認
- 機能性の評価:安全性や操作性、保護性など、強度以外の指標により試験結果を評価
なかでも今回紹介をする耐圧試験は、主に「圧縮強度の確認」を目的として行われます。どの程度のチカラで圧縮すると破壊(破裂、変形、座屈etc.)されるか/基準の圧縮力に耐えることができるかを測定することで、サンプルの物的特性である強度を確認します。
耐圧試験は、保護性能(耐久性、密閉性など)の評価という観点から、パウチ容器やペットボトルなどの包装容器で多く実施されているほか、各種部品や材料などの評価にも用いられています。また、耐圧試験により確認された圧縮強度が、機能性の評価に使用されるケースも少なくありません。たとえば、ペットボトルでは、輸送保管時の耐圧力確認に使われる一方で、廃棄時の潰しやすさという機能性の評価にも耐圧試験が使用されています。
耐圧試験の実施方法
耐圧試験は、別名トップロードテストとも呼ばれているとおり、サンプルの真上から荷重を加える試験です。そのため、試験を行うには、サンプルを圧縮するための仕組みと、チカラを測定するための測定器(フォースゲージなど)が必要です。サンプルの破壊までに大きなチカラを必要としない場合には、測定器を手で持って、サンプルを押し潰すことでも試験は可能です。より大きな荷重値での試験や再現性の高い試験を行いたい場合には、計測スタンドなどと組み合わせて、圧縮試験機を構成します。
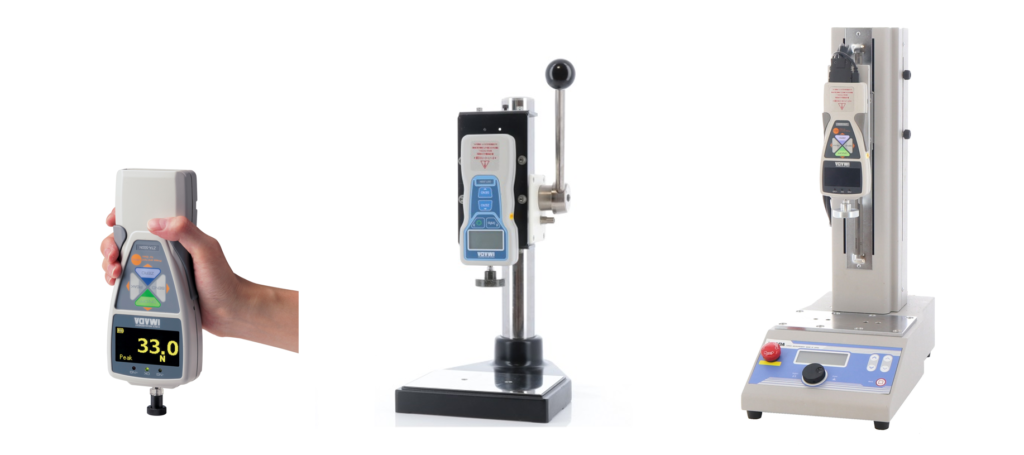
局所的な強度が知りたいなどの理由がない場合には、治具などを使用してサンプル全体を押し潰して強度を確認するのが一般的です。治具の圧縮面がサンプルよりも狭い場合、接触面積や接触箇所が試験結果に影響を与える場合があります。また、圧縮時の押し込み速度なども試験結果に影響を与えます。試験結果を比較する際、合否判定に用いる際には、試験条件にズレがないことに注意が必要です。
耐圧試験(破壊試験)の試験結果は、圧縮力:フォースゲージに表示されるチカラ(N)とは別に、圧力:単位面積あたりのチカラ(Pa)への変換を求められる場合があります。圧力は以下の計算式により、圧縮力と接触面積から計算をすることが可能です。
* Paは1 m2あたりにかかるチカラ(N/㎡)を指します。Pa以外にもN/mm2などの単位が用いられる場合もあります。
* N(ニュートン)はチカラの単位です。1Nで1.02kg程度の重りが乗っている状態の負荷とおおよそ同等です。
破壊試験と耐久性試験
耐圧試験は、大きく「破壊試験」と「耐久性試験」に分類されます。破壊試験は、サンプルが破壊(破裂、変形、座屈etc.)されるまでチカラを加え、破壊されたときのチカラを確認する試験です。一方、耐久性試験は、一定以上のチカラを一定時間加え続けて、破壊されずに耐えられるかを確認します。
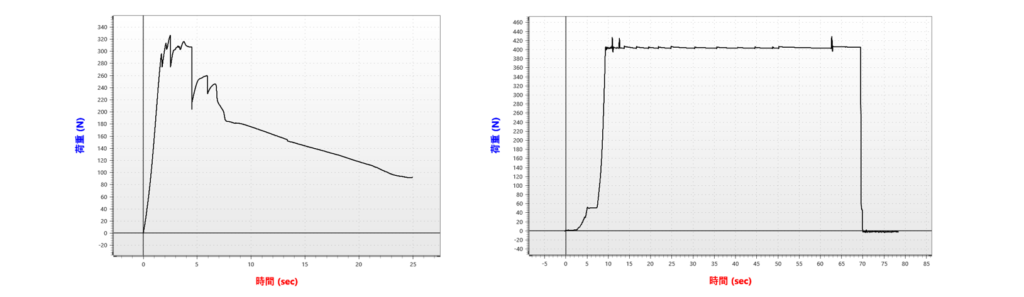
破壊試験では、試験開始後、荷重値が急激に上昇した後に破壊が起こり、荷重値が減少するという荷重推移を辿ります。試験結果=サンプルの耐圧縮強度には破壊が発生した際の荷重値が用いられるため、グラフ描画を行わず、ピーク値*1だけを確認するというケースが多く見られます。一方で、荷重と同時に変位量の測定を行い、破壊が発生した際の押し込み量も確認するというケースも少なくはありません。
耐久性試験では、荷重値と時間が予め決められている必要があるため、社内基準や規格(JIS、ISO、業界規格など)に則って試験をするケースがほとんどです。測定器の代わりに、規定荷重以上の重りをサンプルに載せておこなうことも可能ですが、荷重が全体に偏りなく加わるように注意は必要です。
また、一部のサンプルでは、規定以上のチカラを繰り返し加えて、破壊されずに耐えられるかを確認する「繰り返し耐久性試験」もおこなわれています。
*1 ピーク値とは、測定における最大荷重値を指します。多くのケースにおいて、破壊が発生したときの荷重値が最大荷重値となりますが、部分的に破壊が発生するケースやすぐに底付きが発生するケースでは、破壊後に再度荷重値が上昇する場合があるので注意が必要です。
耐圧試験の事例紹介
先に述べたとおり、耐圧試験は、保護性能の評価という観点から、包装業界で多く採用されています。ここでは、包装業界で行われている代表的な耐圧試験として、「レトルトパウチの圧縮耐久性試験」と「ペットボトルのトップロードテスト」を紹介します。
レトルトパウチ包装の圧縮耐久性試験
レトルトパウチ包装では、その密封性を評価するために圧縮耐久性試験が行われています。
試験では、内容物が入ったレトルトパウチを、一定の荷重で一定時間圧縮して破損や漏れがないかを確認します。荷重や時間については、業界標準やJISなど規格に従うのが一般的です。たとえばJIS Z 0238:1998(ヒートシール軟包装袋及び半剛性容器の試験方法 “10.耐圧縮強さ試験”)では、内容物量により定められた荷重で1分間圧縮すると規定されています。
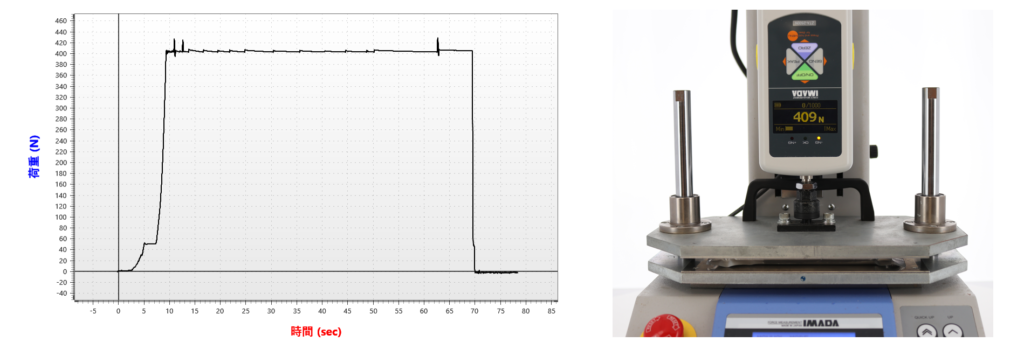
荷重-時間グラフにより規定の時間、規定の荷重値を加わったことを確認できます。
レトルトパウチは変形しやすい容器のため、容器全体を圧縮しないと内容物が圧縮箇所から逃げてしまい、正しい試験結果を得ることができません。正しい試験結果を得るためには、溶着部へしっかりと負荷がかかるように、容器全体を圧縮することが求められます。
>>レトルトパウチの圧縮耐久性試験(JIS Z0238:1998に一部準拠)の試験動画はこちら
ペットボトルのトップロードテスト
ペットボトルの品質管理において、トップロードテスト(耐圧試験)は最も一般的な試験のひとつです。
耐圧縮強度が高まるほど保護性のという観点では優位性が高まりますが、近年ではゴミ量の削減という観点から、あえて強度を下げて潰しやすくした容器も登場しています。トップロードテストは、上記のどちらの観点からも、その優位性を評価するために採用をされています。
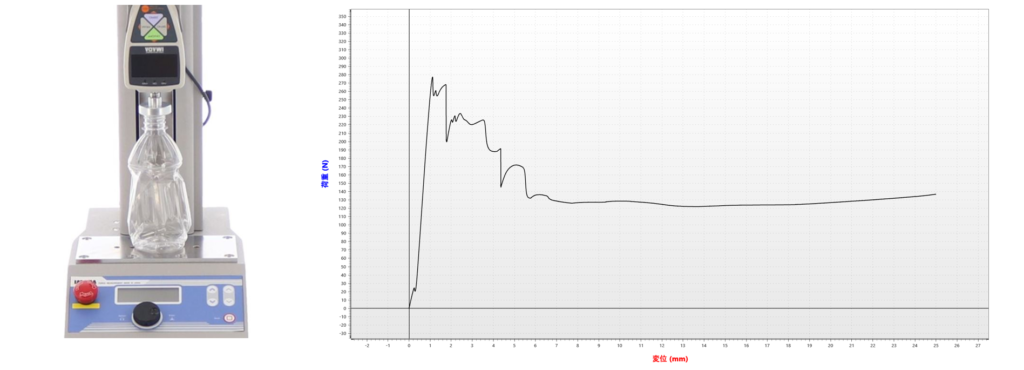
座屈が起きたときの最大荷重に加えて、変位量についても測定するのが、業界として一般的です。
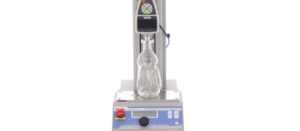
まとめ
今回は圧縮試験のなかでも「耐圧試験」に焦点をあてて紹介をしました。今回紹介した以外にも、曲げ試験や操作性試験、硬さ測定など、圧縮試験の種類は多岐に渡ります。次回は圧縮試験の中でも、材料試験などに多く採用されている「曲げ試験」に焦点をあてて、紹介をする予定です。イマダのHPでは、圧縮試験の測定事例動画を多数公開しています。是非、この機会にチェックしてみてくださいね。