前回の記事では、サンプル全体を押し潰した際の強度を測定する「耐圧試験」について紹介しました。第2回となる今回の記事で紹介をするのは、曲げ(折れ)に対する強度を測定する「曲げ試験」です。
曲げ試験では、両側を支えられたサンプルの中心部に圧縮力を加えることで、サンプルが曲がる(折れる)までに要した荷重値を測定します*1。製品強度の測定という目的ではもちろん、加工性など、材料の特性評価にも利用される試験です。試験方法には「3点曲げ試験」「4点曲げ試験」「片持ち曲げ試験」などの方法があり、用途や目的に応じた適切な試験方法で実施することが求められます。

今回の記事では、各曲げ試験の試験方法を説明するとともに、測定事例を紹介します。
*1 片持ち曲げ試験では、サンプルの片側を支えた状態で、サンプルの反対側に圧縮荷重を加えます。
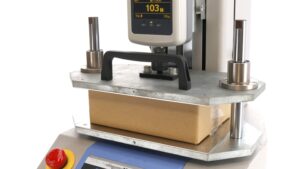
3点曲げ試験と4点曲げ試験
3点曲げ試験は、サンプルの両端を下側で支えながら、中央部にゆっくりと荷重を加えて強度を測定する試験です。支持点2か所と荷重点1か所の計3点で測定を行うことから3点曲げ試験と呼ばれます。4点曲げ試験では荷重点の箇所が2か所に増えて、計4点で測定を行います。
3点曲げ試験と4点曲げ試験の最も大きな違いは、最大応力*2が発生する範囲の違いです。3点曲げ試験の最大応力が荷重点の直下に局所的に発生するのに対して、4点曲げ試験では2か所の荷重点の間に最大応力が均一に発生します。そのため、強度が不均質なサンプル(構造上強度が不均質、表面にランダムな亀裂があるなど)では、3点曲げで強度試験を行うと結果にバラつきが生じる可能性が高くなるため、より再現性の高い測定が可能な4点曲げ試験が採用されています。
*2 応力とは、荷重を受けた物体の内部に発生する力のことです。曲げ試験の場合には、曲げられたサンプルの内部に曲げ応力と呼ばれる応力が発生します。荷重測定では、物体の表面に加えられた力の大きさを測定しますが、実際に物体の内側で発生している力(応力)の大きさは、「物体の形状」や「どこを切り取って考えるか」、「どのように力を加えられたか」に影響を受けます。
3点曲げ試験 | 4点曲げ試験 |
---|---|
![]() 荷重点に応力が集中 | ![]() 荷重点間に一様な応力が発生 |
4点曲げ試験は、強度の不均質なサンプルの測定に適するというメリットを持つ一方で、傾きにより偏荷重が生じやすいなど、試験の難しさというデメリットがあります。そのため、よりシンプルな構造で容易に試験が可能な3点曲げ試験が採用されるケースも少なくなりありません。また、サンプルが小さい場合には、4点曲げ試験を行うことができない場合もあります。なお、3点曲げ試験と4点曲げ試験では、同じ最大曲げ応力を発生させるために必要な圧縮力も異なります。そのため、試験結果を比較する際には、同じ試験方法による結果を比較することが大切です。
3点曲げ試験 | 4点曲げ試験 | |
---|---|---|
測定の容易性 | ◎(シンプルな試験構造) | △(偏荷重が生じやすい) |
最大応力の範囲 | 荷重点の直下に集中 | 荷重点間の範囲で均一 |
不均質なサンプルの測定 | △(測定結果の再現性に欠ける) | ◎(測定結果の再現性が高い) |
破壊までに必要な圧縮力 | 4点曲げより小さな圧縮力で破壊 | 3点曲げより大きな圧縮力が必要 |
その他 | 荷重点のズレの影響を受けやすい | 小さなサンプルの測定ができない |
試験結果は荷重値(N)で表されることもありますが、材料試験などの場合は「曲げ応力(最大応力)」の計算が求められることも多いです。曲げ応力とは、曲げられたサンプルの内部に発生するチカラで、たとえば板状のサンプルの3点曲げ試験の曲げ応力は、下記の計算式によって計算されます。

曲げ応力を計算することで、材料が持つ曲げ特性を評価することができるため、同材料を使用した構造物の強度計算や設計に役立てることが可能です。
なお、曲げ試験では、荷重値に加えてサンプルの変形*3を測定するというケースも少なくありません。曲げ応力と変形量からは、曲げにくさ/曲げやすさの指標である「曲げ弾性率」を計算することができ、材料や製品の剛性評価に活用されています。また、曲げ試験では破壊という現象が起こらないケースも多く、試験結果を比較する際に、サンプルの変形量が評価指標として使わる場合もあります。
*3 変位計を使用したたわみ量(変位量)測定、ひずみゲージを使用したひずみ測定など。
3点曲げ試験の測定事例
3点曲げ試験は、材料特性評価から完成品の強度測定まで幅広く実施されている試験です。ここでは、「ファインセラミックスの3点曲げ強度試験」と「紙ストローの3点曲げ試験」を紹介します。
ファインセラミックスの3点曲げ強度試験
ファインセラミックスでは、材料特性の評価や品質管理に3点曲げ試験や4点曲げ試験が用いられています。たとえば、JIS R 1601: 2008(ファインセラミックスの室温曲げ強さ試験方法)では曲げ強さ(=曲げ応力)を算出するための試験方法として、JIS R 1602: 1995(ファインセラミックスの弾性率試験方法)では曲げ弾性率を算出するための試験法として、3点曲げ、4点曲げの試験条件が規定されています。

ファインセラミックスに限らず、材料特性の評価に関する多くの規格では、サンプルのサイズ(幅、厚み、長さ)や形状から、支点間の距離、支持部や荷重部の形状まで細かく規定されています。必ず規格に準拠しなければならないというわけではありませんが、業界として認知度の高い規格に準拠した試験を行うことで、試験結果に対する信頼性も高まります。
>>ファインセラミックスの3点曲げ強度試験(JIS R1601 :2008 一部準拠)の試験動画はこちら
紙ストローの3点曲げ試験
ストローや鉛筆、歯ブラシなどの細長い製品でも、3点曲げ試験は多く採用されています。
材料特性評価と異なり、試験の規格が定められているケースは少なく、業界標準などが無い限り、試験条件は各企業によって検討を行います。製品が実際に使用される状況に合わせて試験条件が設定されることが多く、あえて荷重部をサンプルの中心から外すというケースも少なくありません。
また変わったところでは、食品の食感試験(硬さ測定)などにも3点曲げ試験が使われています。
いずれにしても、試験結果の比較を行う際には試験条件を揃えた試験の結果を用いることが大切です。

片持ち曲げ試験
片持ち曲げ試験は、片側を固定したサンプルに荷重を加えて、サンプルの曲げ特性を評価する試験です。片側が固定された状態で1点の集中荷重が加わるという製品は、「注射器の針」や「スプーン(カトラリー)」、「釣り竿」など少なくありません。
上記のような事例では、3点曲げ試験や4点曲げ試験では正しい強度測定をすることができず、片持ち曲げ試験によって強度評価を行うことになります。
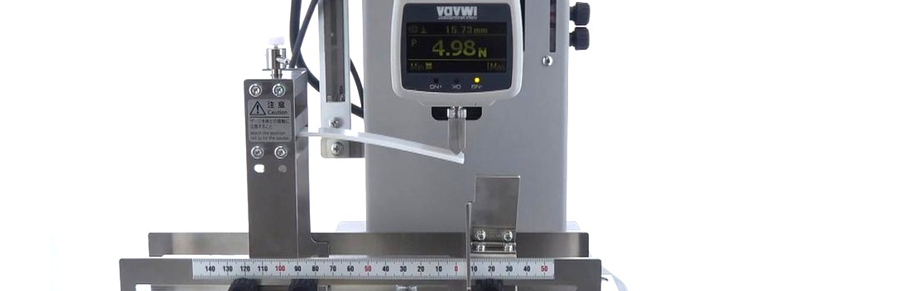
片持ち曲げ試験でも、支点から荷重点までの距離、圧縮力、サンプルの断面積により曲げ応力(MPa)を計算することは可能です。しかし、3点曲げ試験や4点曲げ試験と比べると、片持ち曲げ試験は製品の強度測定に使われるケースが多く、曲げ応力の計算まで行われることはそれほど多くありません。
製品の強度測定を行う場合、実際の使用状況に即して支持位置と荷重位置を決めるのが一般的ですが、やはりその支持位置や荷重位置により測定結果は大きく変わってくることには注意が必要です。
カトラリーの片持ち曲げ試験
脱プラスチックの流れから、プラスチック製のカトラリーは紙製や木製などへと切り替わり、よりシビアな強度管理が求められるようになりました。片側を持った状態で食べ物を載せるというのは、まさに片持ち曲げの状態であり、その強度評価には片持ち曲げ試験が活躍をします。
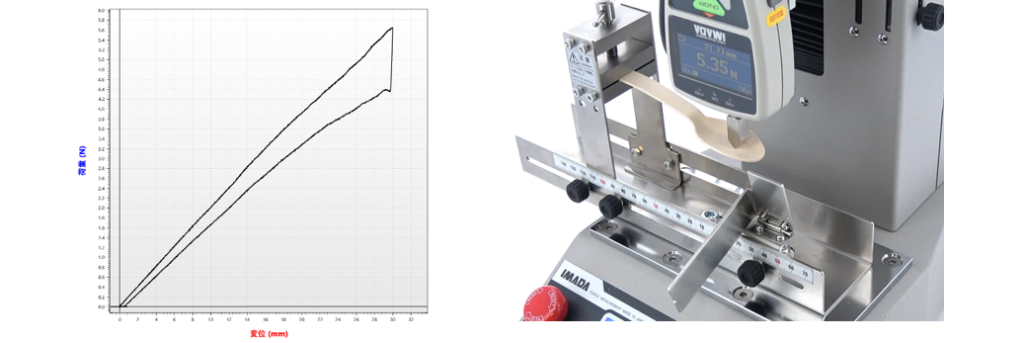
まとめ
今回は圧縮試験のなかでも「曲げ試験」に焦点をあてて紹介をしました。曲げ試験は試験方法が多岐に渡るとともに、曲げ応力や弾性率の計算が求められるケースが多く、非常に奥の深い試験です。圧縮試験には、曲げ試験以外にも、操作性試験や食感測定など、まだまだ多くの試験が存在します。次回は圧縮試験の中でも、操作性試験焦点をあてて、紹介をする予定です。イマダのHPでは、今回紹介した曲げ試験をはじめ、圧縮試験の測定事例動画を多数公開しています。是非、この機会にチェックしてみてはいかがでしょうか?以上、曲げ試験の紹介でした。